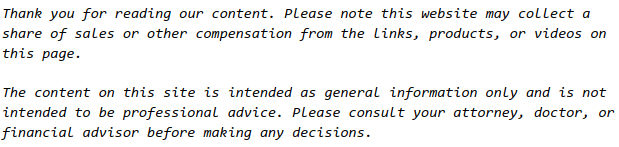
Modern technology has made bicycles, especially the kind found in races like the Tour de France, much lighter than they used to be. But these new lightweight frames constructed from carbon fiber composites are causing major problems for professional and amateur riders alike.
Carbon fiber became popular a few years ago after Greg LeMond, a three-time Tour de France winner, used this material for his bicycle’s frame. The lightweight material contributes to the, strength, speed and aerodynamics of the bikes for their riders.
Yet the bikes’ tough but featherweight construction comes with a serious hazard for riders: the carbon fiber tubing in the bicycles’ frames (and, more recently, wheels) does not bend the way steel and aluminum tubes bend. Instead, the frames and wheels can shatter, causing riders to pitch forward into the road with potentially severe injuries.
The other set of risks won’t harm riders physically but financially instead. Bikes for professional riders can cost between $5,000 and $6,000 USD, and even models created for casual cyclists retail well over $1,000. The most expensive, a model by Trek, is described as the lightest bike frame on the market at 24 ounces and retails for over $15,000.
Mark Greve, a physician and assistant professor of sports medicine at Brown University, told reporters that, “Anyone in a team who’s being honest with you will tell you how frequently their bike are breaking; everyone knows.”
Greve has studied the injuries of 3,500 competitive cyclists and noted that professional riding teams will go through multiple bikes throughout the competitive season because of the wear and tear riders put on them.
So why the silence on the issue from so many pros? The answer is simple: many of these teams and riders offer promotions to the manufacturers of these bikes.
Riders came forward anonymously only to explain the trouble with the carbon fiber bikes. Some said that they would wind up landing on the top horizontal tubes of the bikes when they crashed, falling into the road on a shattered bike frame.
Even bike mechanics described seeing bicycle frames completely destroyed, taken in for repairs in bags that are only meant to hold one bike wheel.
Frames also have to be built in molds as regulated by the International Cycling Union. However, the Union imposed a minimum weight of 15 pounds for the whole bicycle, including the wheels, which leads to lighter and lighter frames produced by manufacturers and could be the reason for the decreasing durability of the bikes.
Part of the onus is also on the manufacturing process for the carbon fiber bicycles. Carbon fiber, like the name implies, is formed as a thread and woven into a fabric.
That fabric is used to be tougher in some spots of the frame, like the cranks, and used less in other parts to allow for greater flexibility. The fabric is coated with epoxy, thus making a plastic bike that’s been reinforced with carbon.
The material, say experts, isn’t made for strength, which also explains the problems that these professional cyclists have during races. Doug Perovic, a professor of materials science and engineering at the University of Toronto, compared carbon fiber to diamonds: they’re both strong but they’re not tough.
Even when manufacturers use multiple layers of carbon fiber, Perovic said, the bike is still at risk for stress and fractures. The metals bend and break into many pieces, often without warning; steel and aluminum bikes, on the other hand, will show signs of wear before eventually breaking down.
The way the carbon bikes are constructed, too, doesn’t rely on the more traditional steel and aluminum tube bending processes long used by manufacturers.
For casual riders who aren’t putting a lot of miles on their bikes, Greve and Perovic both commented that the risk should be minimal for buying a high-priced carbon frame, especially if made by a reputable company.
However, as long as the market demands it, carbon will continue to replace aluminum; steel today is mostly for use in artisan-crafted bike frames.