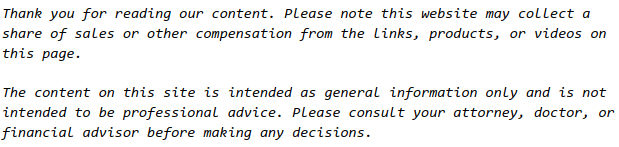
Despite the continuous expansion of the manufacturing industry in the United States, the pace for that growth slowed during the month of May, according to measures of order and production. The Institute for Supply Management, which assesses the expansion of manufacturing, says that the industry is increasing but only at a modest pace.
The ISM said on June 2 that its manufacturing index fell from 54.9 in April to 53.2 in May for the United States. While any reading above 50 indicates expansion, the index has not been that low since February of this year.
Manufacturers are paying higher prices for raw materials right now, as well, which could affect inflation if companies pass on these costs. ISM also said that factories added fewer jobs during the month of May.
However, despite the higher index for April, manufacturing had actually decreased as factories produced less furniture and machinery and fewer plastics, as stated by a mid-May report from the Federal Reserve. The decrease, estimated to be temporary by many economists, had followed two months of strong increases for manufacturing.
The Commerce Department last week said that more long-lasting goods were ordered from U.S. factories in April, but this was mostly due to high demand for military aircraft. Orders unrelated to defense actually fell during the month: weakening core capital goods by 1.2 percent.
This drop is the biggest since the 1.9 percent decrease this past January, after accelerating for a steady six months until a slight dip in December. Before then, U.S. factories produced appliances, automobiles, and other goods consistently.
However, Americans are still purchasing these goods in regular numbers, and businesses are expected to actually spend more on machinery and other equipment in the coming months. This is excellent news for the country’s machine tool industry, which provides mills, lathes, and other computer numerical control products for factories in the United States and around the world. Machine tools are essential in factories where metal and other rigid materials must be cut, bored, drilled, or otherwise fabricated in some way.
Manufacturing has been a leading force in U.S. economic recovery since the financial collapse of 2008. Many jobs are being reshored, returning from offshored jobs, due to the high shipping costs, supply chain logistics, poor quality, and rising labor expenses that have come with offshore jobs in other countries.
But rebuilding those jobs is not without its challenges: today’s manufacturing jobs are requiring more training and education as they become more high-tech. Approximately 80 percent of manufacturing jobs require an Associate’s degree or 12 months of training, according to an Accenture survey of 300 manufacturing executives this past year. The same survey indicates that at least 60 percent of those manufacturers are reporting a severe shortage of highly-skilled workers, however, making this issue one of the greatest obstacles to the current recovery of U.S. manufacturing.