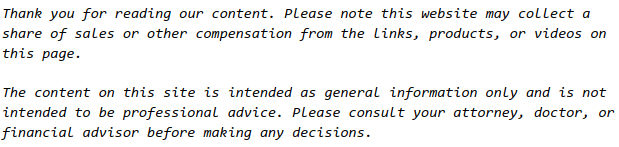
Most load cells utilize strain gauge technology, which is a kind of tech that is very well established and has been a tried and proven method for more than 40 years.
According to CompositesWorld, due to the cost and complexity of strain gage, stress analysts have been forced to focus on the most critical locations and select only a handful of key stress points to instrument with the gages. For example, strain gages have to deal with not only gage sizes, but bonding, attachments, wiring, and more, causing difficulties across various industries.
Now, thanks to fiber-optic sensors, composite designs are going to be much more efficient. Composite designers are now learning that if they can improve component and overall system performance, reliability, and repeatability; they will be able to access even more accurate and essential test and sensor data.
Since the 1990s, fiber-optic sensing has developed, evolved, and matured to a level unmatched within the composites industry. And the future of fiber-optic seems very bright in terms of integrated sensors and other industries.
Additionally, as far as rigid plastics are concerned, compressive testing is perhaps just as antiquated as any other technological method.
According to Quality Info Center, compressive testing can still work and is even necessary in some applications, but it’s not as revered as it once was.
“Compressive testing is just a slower test,” said Steve Driscoll, professor of the department of plastics engineering at the University of Massachusetts Lowell. “Instead of testing at 0.2 inches per minute and up to 20 inches per minute, it’s a very slow test at 0.05 inches per minute. It just takes longer.”
Along with fiber-topic testing, both tensile and flexural testing are becoming commonplace within the composite industry.
“It’s very application and industry-specific,” Driscoll added. “Compressive testing is still very, very critical, just not as popular as tensile testing or flexural testing.”